More than 50 years working in close contact with technicians of the most prestigious foundries in the world has allowed us to create cutting edge products, precise and with extremely contained costs. The need for ever more ground-breaking and precise automation, not easily found on the market, has allowed us to develop our ability to automate and construct specific automatic machines completely within the company. Our internal workshop is equipped with the most modern technologies for the construction of machines, dies, robots and automatic equipment for the production of small metal parts and chaplets for foundry.
Designing and constructing the production equipment, knowing the requirements which the end product must meet has the incomparable advantage of allowing us to calibrate the machine to meet those very requirements. Errors within the process are minimized right from the design and construction stage of the equipment, which will no longer be generic like others on the market, but will respond directly to the strict production requirements of your piece. Reducing errors, more accurate calibration in terms of your specific requirements, observing the relevant tolerances, flexibility in modifications, speed of production and reduction in costs: these are the main advantages of these solutions. Not everyone can offer you that!
Here are the main processing methods which we can provide:
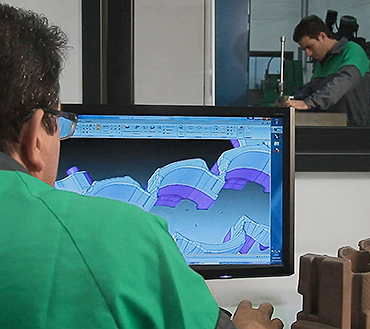
PART DESIGN ASSISTANCE AND PLANNING
It is the at the core of our service. We give everything we have when we work with you, in synergy from the start. We design and plan our equipment knowing the requirements of your part, calibrating the entire production process to the specific part. We study and implement control systems, 100% mechanical and video/electronic to ensure full observance of the design specifications. Our engineers are ready to work in a team, providing the 50 years of experience of our company side by side with the world’s most prestigious car manufacturers.
Put us to the test!
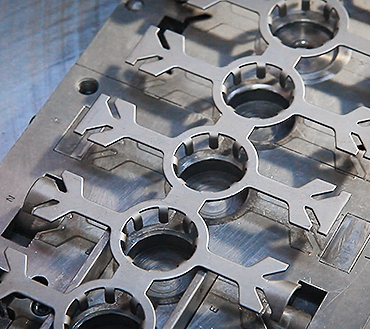
PRESSING
We design and create dies for sheet metal processing. This allows us to be quick and precise with a significant reduction in costs. More than 40 presses of different power levels always ready to press your part.
The dedicated dies, numbered and catalogued, are kept after use, ready for the next job. We regularly shear stainless steel, iron, aluminium, copper.
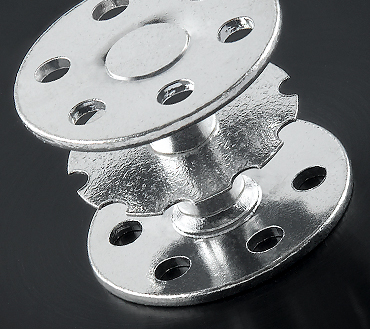
RIVETING
Riveting is the core of the chaplets for foundries. Perfect riveting secures the plates to the stems, preventing them from yielding under the thrust of the casting.
We can guarantee a perfect seal, strong and firm, with no slacking or yielding. With tolerances of less than one tenth of a millimetre. These machines are not available on the market. We have to manufacture them, adding all of our experience.
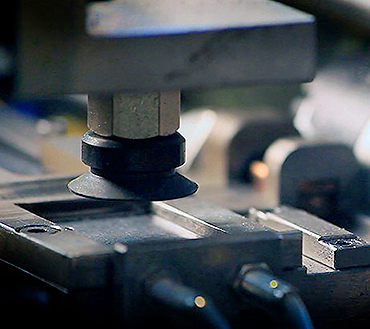
ROBOTIZED ASSEMBLY/AUTOMATION
Parts which are ever more complex and reliable require complicated and costly assembly stages. Automatic assembly and automation, designed and constructed within our plant, allow reliable assembly of semi-processed parts, reducing production costs significantly and ensuring perfect automatic processing, regardless of the characteristics of the operator.
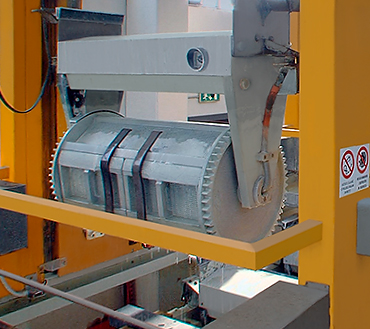
TINNING
Our tinning department is the result of forty years of experience and significant investments which today make it a point of reference in this sector. We have two modern automatic systems for the treatment of electrolytic tinning which are computer controlled and calibrated to our requirements.
The perfect preparation and cleaning of the part, the complete absence of oxidation and optimum tin weldability make the Vemek tinning treatment suitable for all sectors characterised by superior quality and reliability standards.
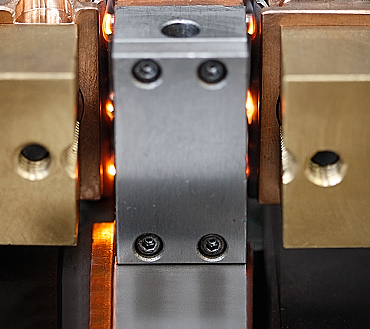
ELECTRO-WELDING
A technology which allows us to firmly join two parts. It is extremely reliable and resistant. It has been used successfully for more than 20 years in core strengthening devices for engines and fusion plate chaplets where it is the only technology which allows us to weld the central plate and ensure pressure-tight casting. The other technologies with through shank and riveting cannot provide the same result.